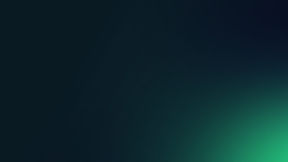

Unlocking the potential of synchrotron X-ray and neutron facilities for industrial advancement
We offer end-to-end materials, process, and component analysis service
We are a team of experts proficient in neutron and synchrotron techniques, materials science, data science, and software development. Collaborating closely with you, we understand your specific needs, select the optimal neutron and synchrotron X-ray characterization technique, and conduct thorough data analysis using our continuously evolving software: Scatterin SaaS.
Our expertise enables us to support and guide you through demanding diffraction, small-angle scattering, and imaging experiments, ensuring both compliance and optimal performance for your specific needs.
​
How we help
Our service enables companies to significantly reduce the time required for materials, component, and process analysis. By leveraging our technology, our clients attain exceptionally high-quality analysis results that were previously unattainable with traditional lab-scale techniques.
​
The outcome
Our approach helps companies to streamline R&D processes and quality control measures, resulting in significant time and cost savings. By accessing previously unattainable information, our clients boost their capacity for innovation and competitiveness within their industries.
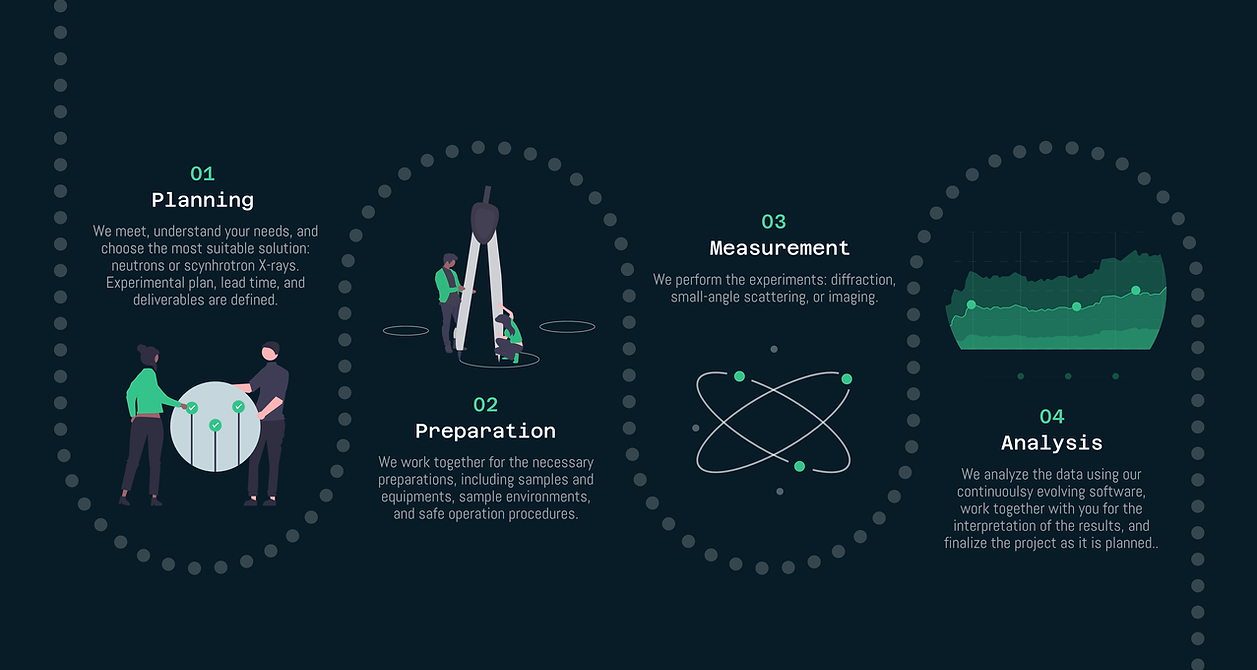
Services
and deliverables
01
Residual strain/stress measurements
Residual strains and stresses in real industrial components are measured using neutron and synchrotron X-ray diffraction techniques.
-
Only techniques enabling non-destructive 3D mapping of residual stress gradients.
-
Penetration up to 7 cm in steel.
-
Measurements in tri-axial residual stress condition.
-
µm-level resolution can be reached in mapping.
03
Quantification of defects
Deformation behavior and defects, e.g. dislocations and stacking faults, are quantified by neutron and synchrotron X-ray diffraction.
-
In-situ measurements during deformation or cycle within a large temperature range with <1 second time resolution can be performed.
-
µm-level resolution in structural mapping.
05
Available equipment for simulation of process and service conditions
-
Quenching and partitioning dilatometer
-
High-temperature and cryofurnaces
-
Electro-Thermal Mechanical Testing System
-
Deformation rigs for wide temperature range
-
Various reaction chambers and electrochemical cells.
02
Quantification and identification of phases and precipitates
Minority phases, e.g. retained austenite, and precipitates are identified and quantified by neutron and synchrotron X-ray diffraction and small-angle scattering techniques.
-
In-situ measurements in mimicked processing and service conditions with <1 second time resolution can be performed.
-
Minority phases and precipitates (<1 vol%) can be detected.
-
µm-level resolution can be reached in structural mapping.
04
Imaging and tomography
Dynamics of processes and movements in working equipment can be imaged and quantified in-real time with time resolution better than 1 ms by neutron and synchrotron X-ray radiography.
Defects and other features inside materials can be reconstructed and quantified with resolution better than 1 µm.
06
Bringing own equipment and large components
If your requirements extend beyond the capabilities of existing sample environments and equipment at neutron and synchrotron X-ray facilities, we facilitate the arrangement of necessary technical and safety provisions. Whether it involves integrating your proprietary equipment—such as furnaces, battery cells, or specialized working parts like engines—or enhancing the existing setup, we ensure seamless coordination.
Our experience includes adeptly navigating and complying with the stringent technical and safety regulations governing neutron and synchrotron facilities.